-
| Engineered for excellence
In the press shops of the automotive industry, more than a million car body parts of various shapes and sizes for multiple models are produced every day. Due to this high variance press die set needs to be changed frequently requiring shorter press-cycles. Hence the slinging of the press dies with conventional slinging equipment such as chains or ropes is being replaced with die grippers enabling fast, compact, and multi-level storage of the pressing dies.
Konecranes Die gripper cranes is custom designed for die handling application in automotive industry. Die gripper crane is available with trolley equipped with coupled winches, intelligent sensor technology, advanced smart features, precise positioning system helping in high-performance, efficient, and safe transport of press dies. -
Technical specification


Features
• Trolley with coupled open winches
• Design of all components considering a centre of gravity eccentricity of 100mm, related to the max. die weight
• Stable 4-point load suspension with balancing rocker
• Millimetre-precise pendulum-free positioning
• Redundant laser or barcode measuring systems
• anti-sway control
• Die gripper with integrated slewing gear.
• Uniform utilisation of the rope strands due to integrated compensating rocker.
• Ropes tested for this application with high structural stability and high breaking load.
• Optional rope drive
• Synchronised sensors designed redundantly and are evaluated in a fail-safe programmable logical controller (PLC).


Benefits
• Faster die change
• Safe die handling (pick-up, transport and drop off)
• Efficient, space-saving utilisation of the available storage area
• Cranes and die grippers are customised as per customer requirements
• Optimised reeving with a minimum of rope sheaves gives a maximised rope service lifetime.
• Different level of automation possible: From manual operation to semi-automatic to fully automatic in combination with the Konecranes Warehouse Managing System.
• Intelligent sensor technology recognises safe load pick-up and detects the surrounding area of gripper to avoid collisions.
• All safety-relevant functions are controlled in performance level d (PL d), category 2, according to EN ISO 13849-1. This also includes the bypassing of restrictive areas and route-guided target positioning.
• Crane and WMS Status visualisations on mobile devices
• Excellent accessibility to all components for maintenance and service activities.
• Remote maintenance capability for quick problem solving and preventive maintenance planning.
Technical specification


Features
• Trolley with coupled open winches
• Design of all components considering a centre of gravity eccentricity of 100mm, related to the max. die weight
• Stable 4-point load suspension with balancing rocker
• Millimetre-precise pendulum-free positioning
• Redundant laser or barcode measuring systems
• anti-sway control
• Die gripper with integrated slewing gear.
• Uniform utilisation of the rope strands due to integrated compensating rocker.
• Ropes tested for this application with high structural stability and high breaking load.
• Optional rope drive
• Synchronised sensors designed redundantly and are evaluated in a fail-safe programmable logical controller (PLC).
We chose Konecranes for a good overall package with quality and punctuality. Cooperation secured the original goals for safety and ease of operation.
Anders Boking, Manager, Production Planning, Volvo Car Corporation, Olofström, Sweden
Smart features included in basic die gripper crane
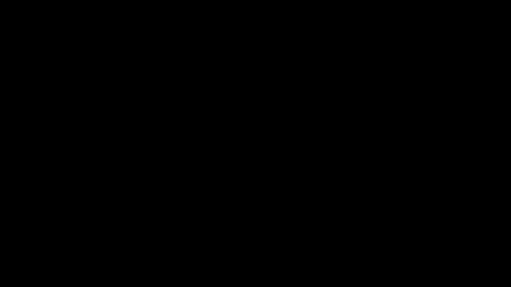
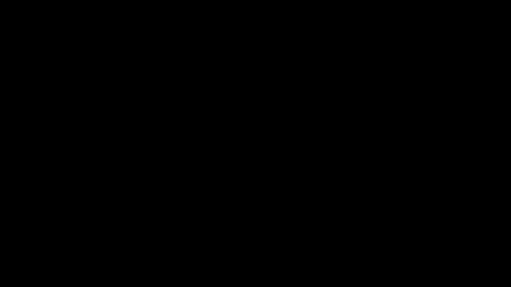
Protected Areas - Optional
Possible obstacles, such as the press, try-out press, offices or work areas, are taken into account when determining the transport routes from the die storage to the press as a bypass area, executed in safe performance level D.
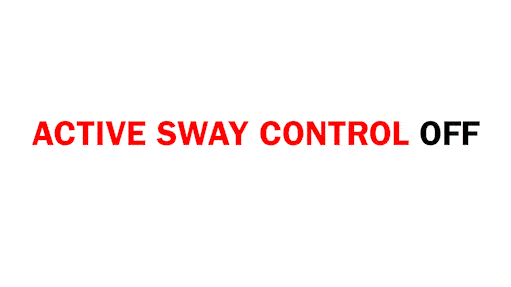
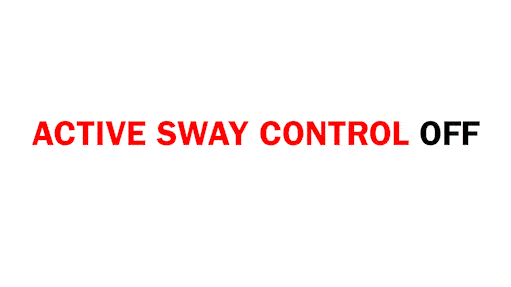
Active Sway Control
Sway Control limits load swing by controlling the acceleration and deceleration of the bridge and trolley, enabling faster load handling and more precise positioning. Active sway control automatically eliminates load swing during crane operations. Based on the continual measurement of angle between trolley and gripper, it fine-tunes the speed commands and stabilizes load movement in trolley and bridge travel including rotational control and skew compensation. The anti-sway system provides functions, which go far beyond simple sway damping:
• Perfect control of the load oscillation in all driving situations
• Simultaneous motion of hoisting, long and cross travel and slewing gear rotation without any restriction
• Highest precision at maximum driving dynamics due to short internal cycle times
• No overshoot - stop without reversing. Virtually complete elimination of sway at stop
• No residual sway
• Very high target accuracy of less than ± 10 mm at the load
• Very high load rotational angle control accuracy of less than ± 0,2 deg. at the load
• Automatic mode at any lifting height
• Automatic circumnavigation of restricted areas
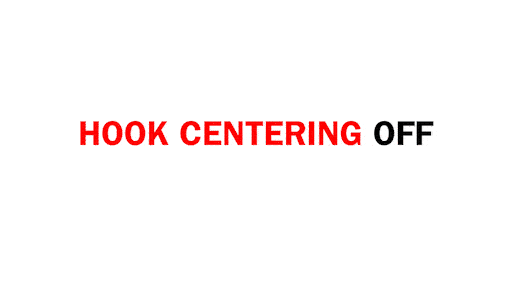
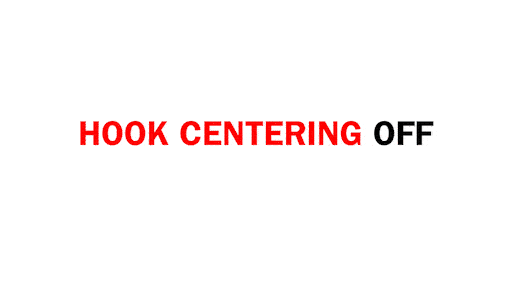
Hook Centering
Hook Centering feature eliminates side pull and load swing caused by side pull. When the die gripper is coupled, the hook centering system ensures that the load can only be lifted when it is directly vertical under the trolley. The vertical angle as well as the rotation angle are determined by a camera-reflector system and compensated by the control system.
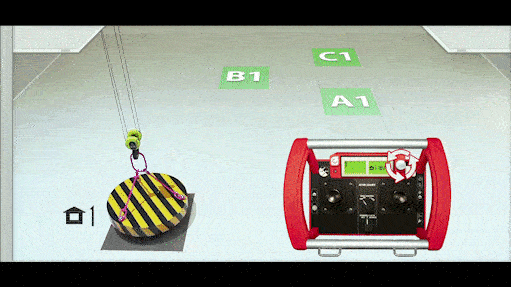
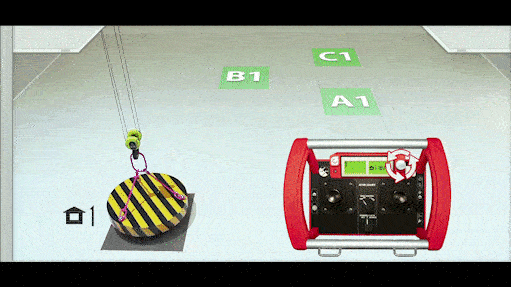
Target Positioning - Optional
Target positioning moves the load along a pre-determined route from an initial position to a selected target position. The operator selects the target position via the radio control, presses a button, holds it down and the crane moves to that position. This reduces work cycle times and the risk of human error in repetitive operations.
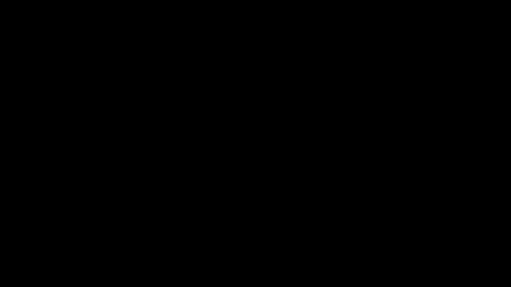
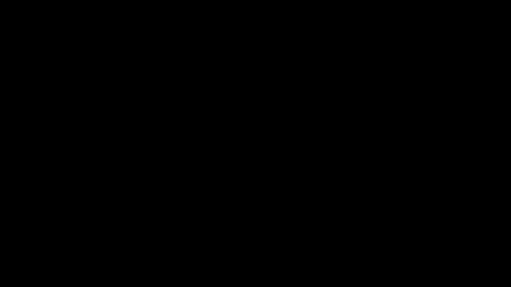
Protected Areas - Optional
Possible obstacles, such as the press, try-out press, offices or work areas, are taken into account when determining the transport routes from the die storage to the press as a bypass area, executed in safe performance level D.
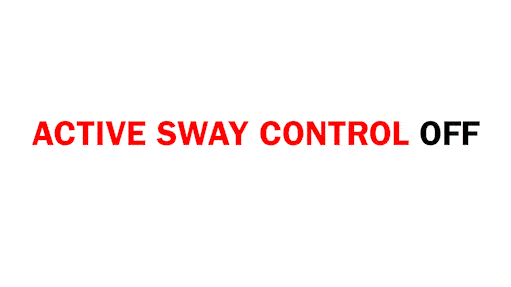
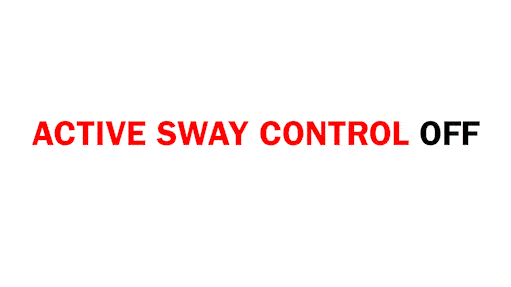
Active Sway Control
Sway Control limits load swing by controlling the acceleration and deceleration of the bridge and trolley, enabling faster load handling and more precise positioning. Active sway control automatically eliminates load swing during crane operations. Based on the continual measurement of angle between trolley and gripper, it fine-tunes the speed commands and stabilizes load movement in trolley and bridge travel including rotational control and skew compensation. The anti-sway system provides functions, which go far beyond simple sway damping:
• Perfect control of the load oscillation in all driving situations
• Simultaneous motion of hoisting, long and cross travel and slewing gear rotation without any restriction
• Highest precision at maximum driving dynamics due to short internal cycle times
• No overshoot - stop without reversing. Virtually complete elimination of sway at stop
• No residual sway
• Very high target accuracy of less than ± 10 mm at the load
• Very high load rotational angle control accuracy of less than ± 0,2 deg. at the load
• Automatic mode at any lifting height
• Automatic circumnavigation of restricted areas
Expertise that makes a difference
By working closely with customers, Konecranes has developed a body of experience in automotive industry processes and material handling applications. By applying our expertise, advanced technology, and service offerings, we can make a difference in the safety and productivity of your operation. Get in touch with our experts to learn more about our smart die gripper cranes.