Becoming carbon neutral is a gradual process of realistic steps at every phase of the lifting lifecycle. For Konecranes, this means presenting our industry with a guided path towards ecolifting. We have closely studied our own and our customers’ operations to determine the incremental steps that can be taken to reduce carbon impact at each stage.
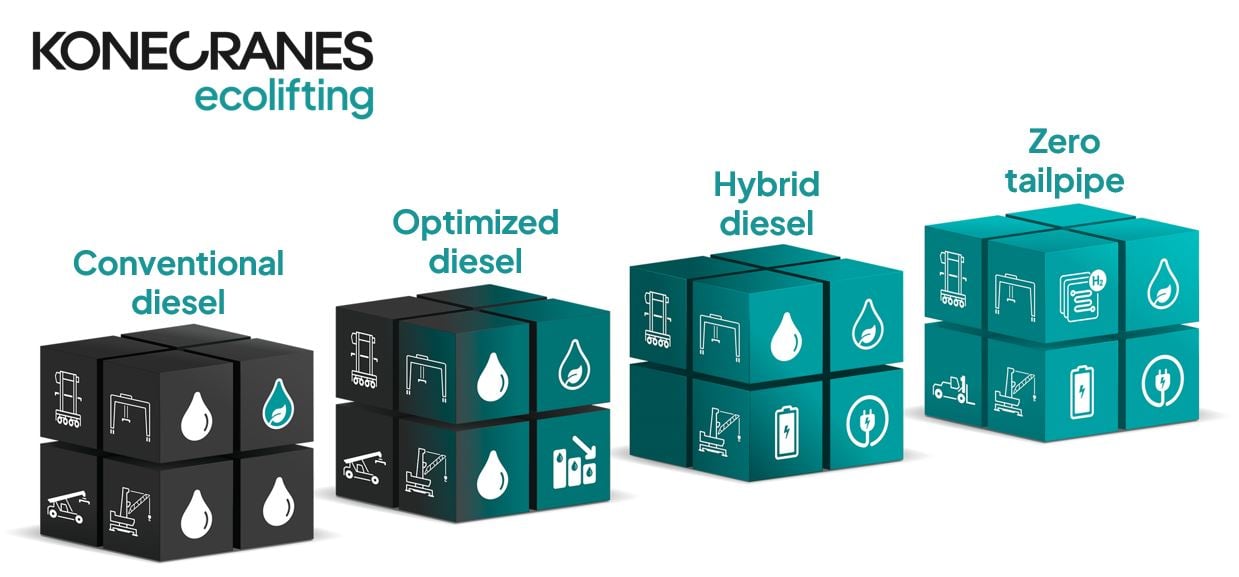
The transition for a port operator could start with assessing available energy options and choosing low- or zero-carbon alternatives. When a terminal shifts from energy generated by fossil fuels to energy from renewable sources – such as solar, wind or hydro power – the impact is felt both seaside and portside. Vessels can refuel with cleaner options and terminal equipment can be operated with low- or zero-carbon impact.
Konecranes’ own journey starts with our manufacturing process and the raw materials we use. As we said in our Sustainability Report 2023, we aim to collaborate with steel suppliers who share our ambition to minimize emissions. In another step towards reducing Konecranes’ own carbon footprint, our Port Solutions factories now use 100% renewable electricity.
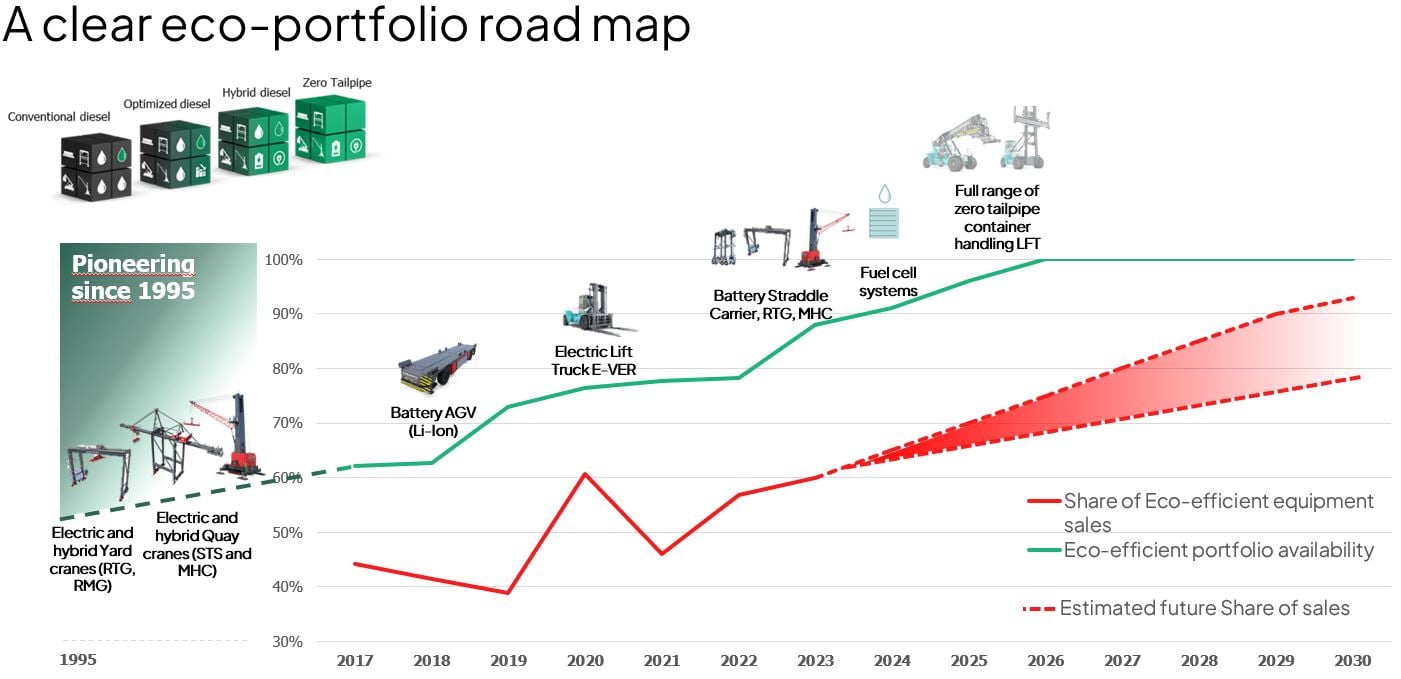
While these are positive steps, it’s the use phase of our products where the heaviest carbon impact is registered. This is why Konecranes has committed to offering fully electric variants of our entire product portfolio by 2026. We are also focused on developing pathways and solutions that help our customers to reduce the carbon impact of their diesel engines.
“Switching to biofuel significantly cuts the CO2 emissions of a diesel drive, so this is a good place to start. Then you can look at optimizing the equipment with solutions like Konecranes Power Drive and Flow Drive for lift trucks, or biofuel suitable variable-speed diesel engines for RTGs,” explains Matti Talala, Regional Sales Director, APAC at Konecranes.
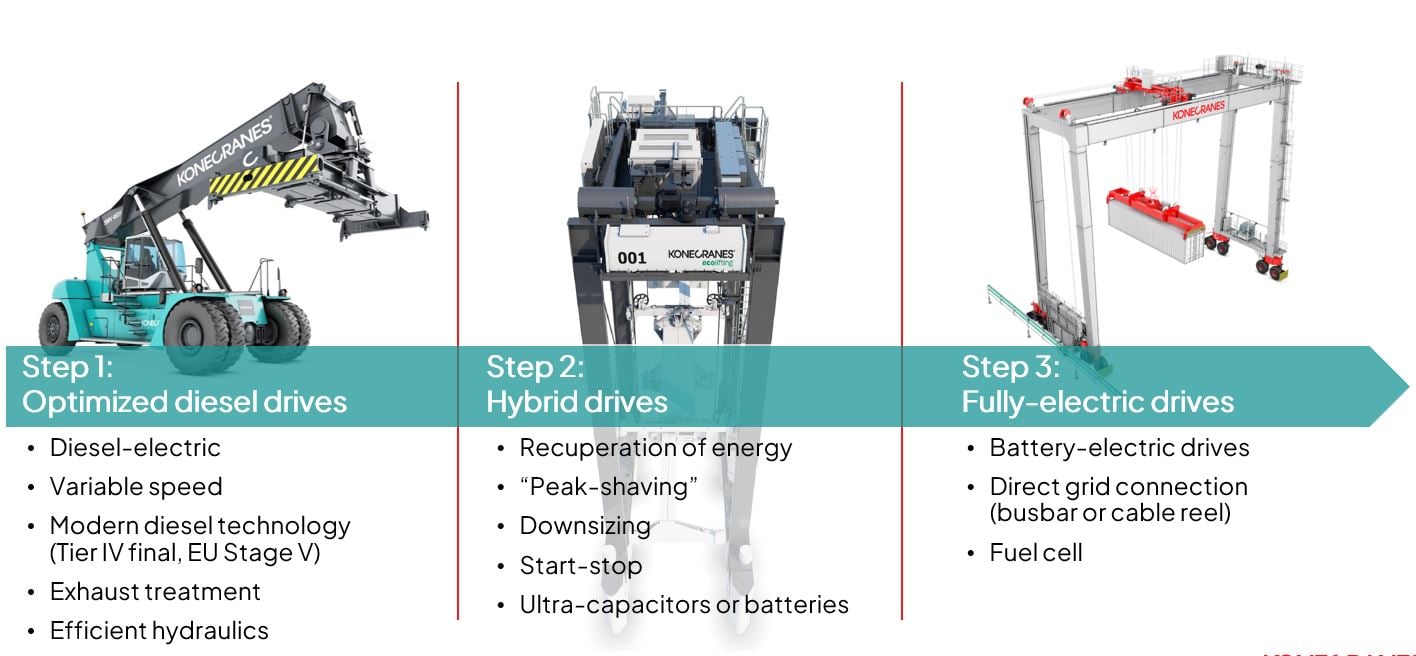
“The next step is to introduce a Konecranes hybrid drive. It is an optimally sized combination of lithium-ion batteries and diesel-generator set,” he says. “One of my favorite things about hybrid drives is that it allows to capture the excess energy – such as that generated when lowering a hoist – and pushes it back to the batteries to utilize the energy in the next operational cycle.”
The most advanced step on the path to eco-lifting is to introduce so-called ‘zero tailpipe’ equipment, where no CO2 is generated in the use phase. For example, Konecranes fully electric drives can be connected to the grid with a cable reel in ports that have the necessary mains infrastructure.
“It's important to note that Konecranes eco-efficient solutions and upgrades can be retrofitted to equipment from other manufacturers too. In this way crane owners can protect their investment while moving further along the path towards ecolifting,” explains Talala.
Konecranes machinery is also ready for the hydrogen solutions that are starting to emerge on the market. We are currently exploring the two main development streams for this technology – i.e. hydrogen as a direct fuel, and hydrogen fuel cells – for the next step in moving our industry towards net zero.
Konecranes works for a decarbonized and circular world for customers and society. We are helping to build the means to get there for our customers, step by step. At Konecranes Port Solutions we call this Ecolifting™: a systematic movement towards lower CO2 per container move. Today, all Konecranes factories globally use renewable electricity and we are committed to cutting our global emissions in half by 2030.
Related materials: