Sam Procter gives us the "nuts and bolts" of ongoing advanced port services product development. Sam is an experienced Konecranes MHC technician, who is now an essential member of our Advanced Port Services product development team.
Q: Welcome Sam, thanks for your time. Let’s jump right in, you’re a crane engineer with a specialty in mobile harbor cranes. But what are you doing now?
A: I took advantage of internal opportunities that arose in the Port Services unit, specifically in the digital development team, and now apply my hands-on experience to ensure that our predictive services capabilities, as well as our maintenance management software solutions, are fit-for-purpose and solve equipment maintenance issues on the ground.
Q: How’s that going?
A: So, we are at a really exciting stage at the moment, we have predictive services projects running concurrently. We have also harmonized the design of our system architecture to suit all generations of MHCs, from retrofits to new installations, with the first factory-fitted predictive system being delivered within the next few weeks. We are also refining improved data visualizations for swift decision-making. So in short we have put in the hard miles so that customers have a frictionless experience with any of our advanced services.
Q: Which port equipment are you leading with?
A: We launched the predictive services product in April this year specifically for mobile harbor cranes, and the AMMS system is ready for any equipment, even other brand cranes. With predictive services we have now partnered with a number of customers on deep-dive data gathering across critical components on other equipment types and those services will be launched really soon.
Q: You’ve also spent quite a bit of time on the new AMMS, tell us a bit more about that product.
A: We see AMMS as a service rather than “just” a product. What I mean by that is that some customers already have a CMMS – computerized computer maintenance system – and aren’t necessarily in the market for another one. So, we can either come in, from an equipment point of view, and enable any CMMS system the customer has, or we can provide a turnkey solution that includes a CMMS platform. That’s why we call it AMMS Advanced Maintenance Management Services because it goes beyond software to actually tie the whole maintenance planning system, skill sets and equipment together as a total service to customers.
Q: It doesn’t sound that simple, I mean equipment breaks, we go in and fix it – that I can understand. But how is software and data going to make mechanical differences to real cranes, and why should customers pay for that service?
A: I agree it’s a mindset change, certainly. The most important concept to grasp is that our equipment produces huge amounts of data, every shift. Whether that’s usage data, or data generated by components and systems on the crane. So, we either capture and leverage that data to get insight into the equipment’s current and future condition, or we don’t. And, because we’re Konecranes and we have a responsibility to our customers, we have decided to invest in these systems and knowledgebases now, even though it’s not standard across the industry yet. Knowledge is key, and knowledge backed up by data is limitless.
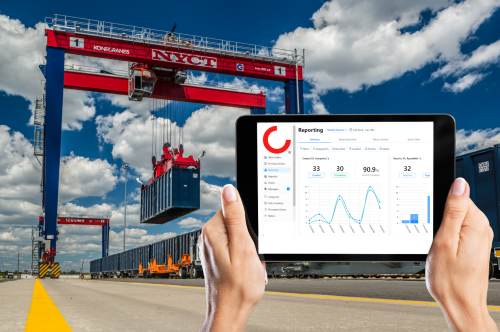
Q: Right, so it’s about offering customers something they may not even know they want yet?
A: In a way I guess so. Although I can assure you that the mechanics, engineers and technicians on sites across the world know that if they had better individual crane data and live equipment information available in one place, mobile-enabled and regularly updated by the OEM they could focus 100% more on problem-solving. And that’s what AMMS can do; from a maintenance management point of view I’m convinced it’s a port equipment paradigm shift.
We have put in the hard miles so that customers have a frictionless experience with any of our advanced services.
Q: So Konecranes is taking an open-source approach to the equipment data and information, in a way?
A: Exactly, there’s now an understanding that the more we empower technicians on the ground with information and data, the faster and better their problem solving will be. Obviously nine times out of ten, most problems can be resolved just by supplying some basic information, but it's providing that information in a useful way that’s critical. Even something as simple as having crane manuals on mobile applications, as we are doing with the AMMS, is a real game-changer.
Q: And I guess ultimately data flows both ways as well. So, the more a customer, or their team uses it, the better the system’s data and output becomes.
A: Yes, that’s key! Because there's so many people that will be called out to that crane and everyone's very busy all the time, jumping from one job to the next. So, to be able to quickly input information of what you found on the crane, and it’s there for everybody to see in future, a pragmatic way to share fault information between teams is part of the teamwork side. It's about gathering all that data together in one platform which allows anybody to go to that crane and say, yeah, this was the problem before.
Q: Cycling back to Predictive Services – what’s the next developmental step there?
A: OK, so there are two things: Firstly, we are producing internal knowledge systems so that we can fully scale installation and maintenance of the product across our global Frontline network.
Secondly, we are running the analytics for the pilot projects, which is another crucial learning curve, which becomes more dynamic and complex as time goes by, and the components change. We are becoming component experts now, as we look at the data and learn how each item or material is meant to work over time, it’s a huge investment in our knowledgebase. At the same time we are evolving the reporting and data presentation methods beyond simple pdfs.
Q: So, outside of what we may learn from our component suppliers, Konecranes is creating its own benchmarks regarding temperature or vibrational data on critical components?
A: Yes, and that’s the knowledge you can't buy. It’s not available even from the OEMs. So we have had to start from scratch in building that intelligence. Whether its adjusting alarm levels on software to see when we are getting these vibrations and working out whether there are a common problem or are they outliers, and then adjusting the software to suit.
Q: Thanks so much Sam, you are certainly in a whole new world of problem solving than you were before. One final question: do you ever miss running around up and down the gantries?
A: Depends what day of the week it is. 😊