Smarter where it matters
When it comes to choosing the right level of automation, it’s important to understand the nature of what you are machining as well as your specific requirements and capabilities. While fully automated systems can provide a cost-effective option, a semi-automated solution may be better suited to meet production goals.
Konecranes Smart Features are advanced crane software that gives you more control over your lifting and increases productivity by saving time and money with shorter load cycle times, reducing wear and lengthening the crane’s life cycle with crane movement optimization, and improving safety by decreasing the chance of human error.
Load control
Load Control Features are designed to improve the crane operator's safety and productivity by making the crane move more smoothly and easily.
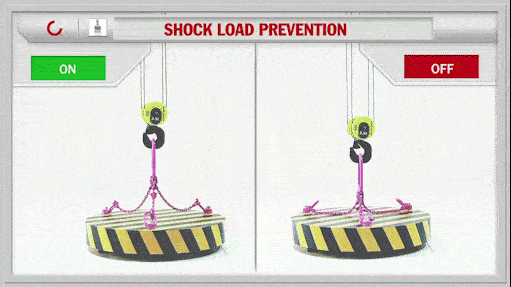
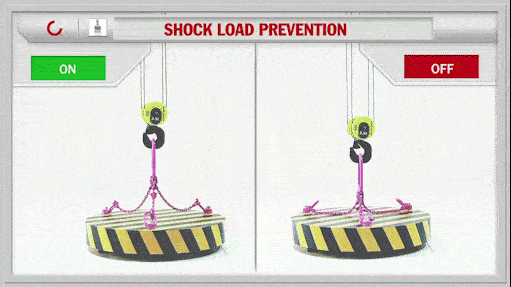
Shock Load Prevention
Shock Load Protection is designed for smooth load pickups and to prevent shocks to the load and the crane. It is a feature of Konecranes Variable Frequency Drives for hoist control. If a load is picked up too fast, the hoisting speed is automatically reduced until the load is raised. This protects the crane and reduces the risk of collision and damage to buckets, hoppers and pit walls. With this automated feature, the operator can focus on controlling the load, monitoring his or her environment and ensuring that the load remains secure.
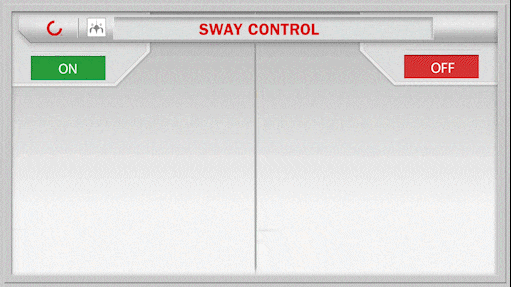
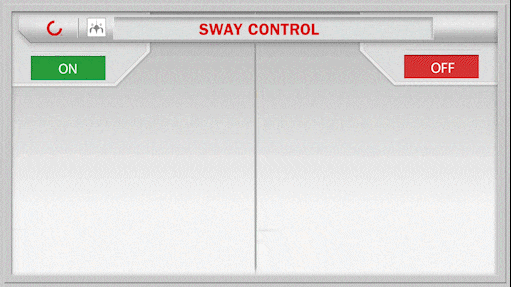
Sway Control for Waste to Energy
Sway Control limits load swing by controlling the acceleration and deceleration of the bridge and trolley, enabling faster load handling and more precise positioning. The operator can use full crane, trolley, and hoists speeds even while driving close to the walls, and the risk of grab damage is reduced.
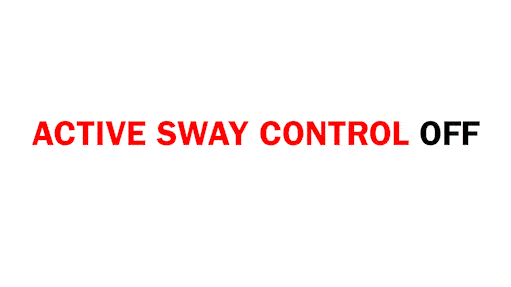
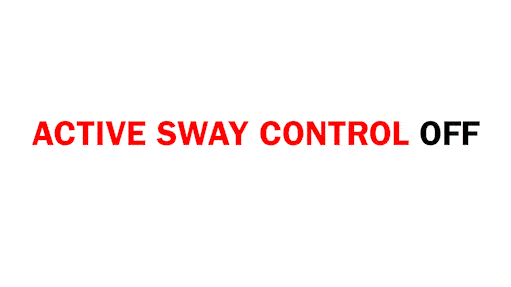
Active Sway Control
Active Sway Control is available for standard duty biomass cranes only. It automatically eliminates load sway during crane operation. Based on the continual measurement of the rope angle, it fine tunes the operator’s speed commands and stabilizes load movement in both trolley and bridge travel. Minimal load sway throughout the duty cycle improves operational safety, load cycle times, ease of crane operation and reduces wear on crane components.
This feature is only available for CXT hoists
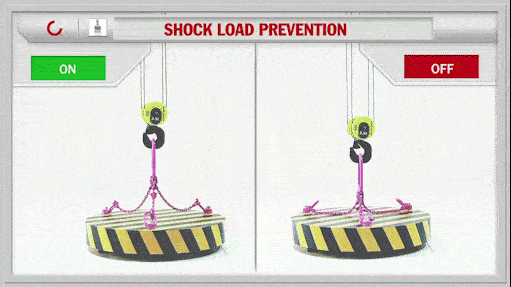
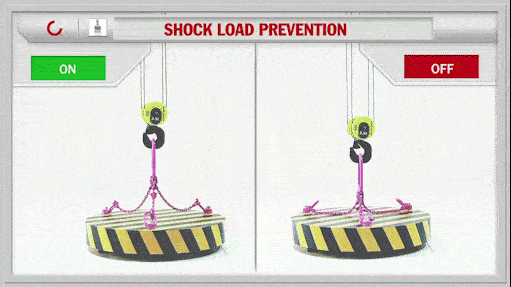
Shock Load Prevention
Shock Load Protection is designed for smooth load pickups and to prevent shocks to the load and the crane. It is a feature of Konecranes Variable Frequency Drives for hoist control. If a load is picked up too fast, the hoisting speed is automatically reduced until the load is raised. This protects the crane and reduces the risk of collision and damage to buckets, hoppers and pit walls. With this automated feature, the operator can focus on controlling the load, monitoring his or her environment and ensuring that the load remains secure.
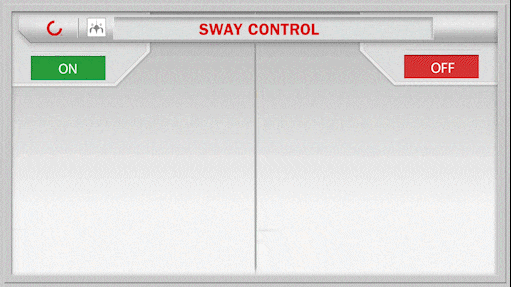
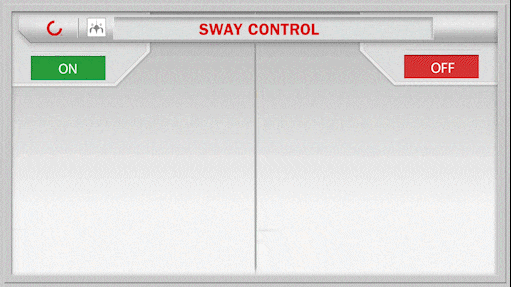
Sway Control for Waste to Energy
Sway Control limits load swing by controlling the acceleration and deceleration of the bridge and trolley, enabling faster load handling and more precise positioning. The operator can use full crane, trolley, and hoists speeds even while driving close to the walls, and the risk of grab damage is reduced.
Area control for maximum productivity and efficiency
Smart Features also give you more control over the working area of the crane, improving the efficiency and accuracy of load positioning by adapting the available space to the physical layout of your production line.
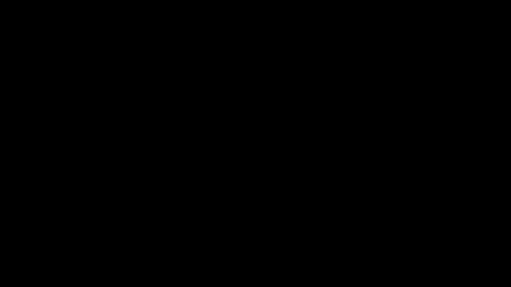
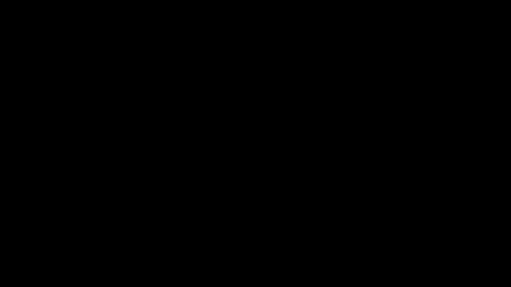
End Positioning
End Positioning allows operators to set the exact destination of a load and the outside area, or “window” for manual navigation. Once the operator brings the crane to the window, the End Positioning button automatically sends the crane to its final position. As a safety feature, the operator lowers the load manually to complete the movement.
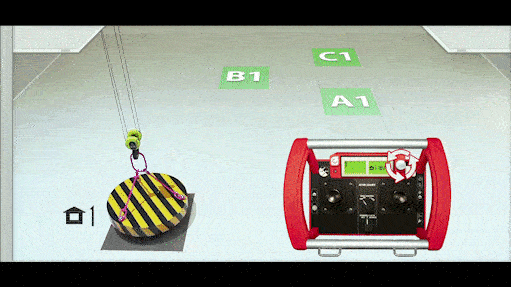
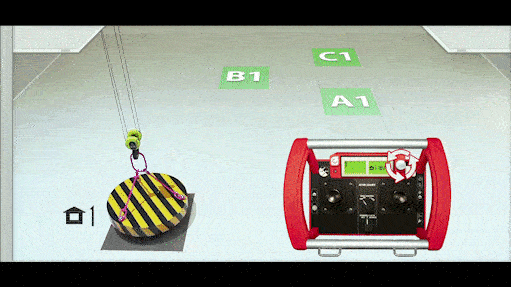
Target Positioning
Target Positioning moves the load from one of eight home positions to one of 120 possible preset target positions within a predefined area. The crane slows down, stops and lowers the load at the set target point. Just one button automatically returns the crane to its home location.
The Konecranes Target Positioning feature has been designed to reduce cycle times and to enhance safety.
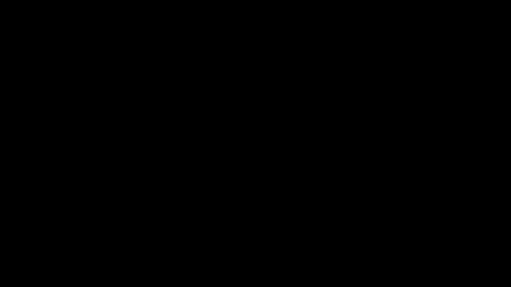
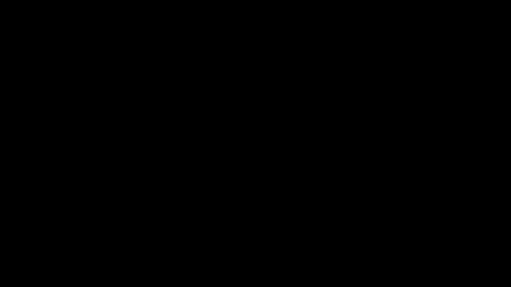
Protected Areas
Protected Areas allocates up to 16 permanent “no-go” zones to limit the crane’s movements to preset working areas only. This feature maximizes crane operating space, while helping to reduce the risk of accidents, equipment collisions and load damage.
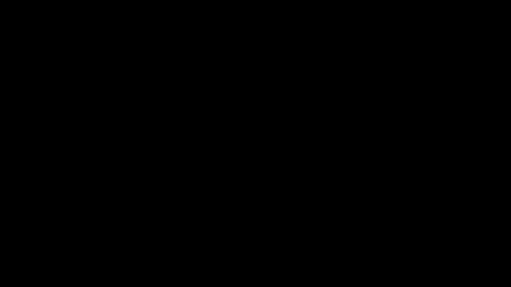
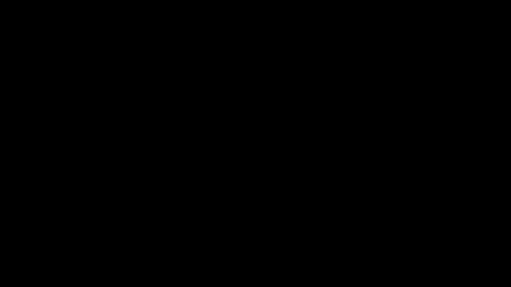
End Positioning
End Positioning allows operators to set the exact destination of a load and the outside area, or “window” for manual navigation. Once the operator brings the crane to the window, the End Positioning button automatically sends the crane to its final position. As a safety feature, the operator lowers the load manually to complete the movement.
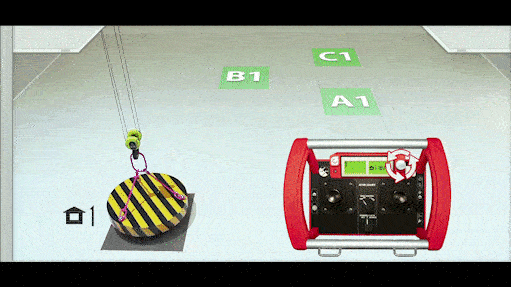
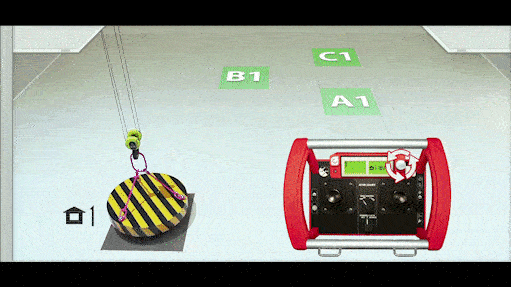
Target Positioning
Target Positioning moves the load from one of eight home positions to one of 120 possible preset target positions within a predefined area. The crane slows down, stops and lowers the load at the set target point. Just one button automatically returns the crane to its home location.
The Konecranes Target Positioning feature has been designed to reduce cycle times and to enhance safety.
Intelligent automation has revolutionized waste treatment and incineration technology.
Petri Onikki, Technical Director, Ekokem
Safety and functionality enhanced
Konecranes is known worldwide for creating and promoting modern lifting technology. With extensive experience in waste and biomass handling processes, we understand the demands of waste handling and the importance of reliable and advanced lifting technology.